I love to print my art and designs, but I also use the equipment in my studio to do custom print collaborations. I work with all sorts of visual artists. musicians, poets, concert venues, small businesses, and folks who simply want to create ephemera for a special occasion. I can brainstorm, develop projects, and make designs for clients. I can also be hired to print pieces in their final stage of realization, and it’s exciting to work with designers and illustrators directly as their printer. Also, a collaboration might be with multiple people, such as with a bride-to-be and her best friend who is a graphic designer, in that situation my role is simply being the master printer who shares advice and expertise while getting their project ready to go on one of my presses.
There are multiple things that Stukenborg Press can do for you; that pun is relentlessly present. Rarely, making one or even just a couple of something is ever going to be cost-effective. Most of the time and work for letterpress projects occurs during preparation and set-up. Sketches, design, typesetting, plate-making, carving, ink mixing, and proofing; all these things happen before the first good print is pulled off the press. Doing custom letterpress work is a bit like making a batch of cookies. If you want a special kind that has your unique combination of ingredients, it is only reasonable to get a whole batch, otherwise, you’ll be paying for all the design, setup and presswork to be held within one single unit. Edition sizes are commonly between 100 and 250, but there are of course projects that can warrant smaller or larger numbers. All of the work I do in the studio for people is custom and fit to suit their needs, there aren’t any templates being used so the work will always be fresh and new.
Determining the cost of a project requires consideration of the materials used in the project, and all the aspects of labor required to set up, print, and finish the edition. Because every project is unique, a quote for pricing will only be given after a preliminary discussion is had.
After all the design work is finished and the printing begins. The time it takes to complete the printing of a project depends more on the number of passes of color in a design, rather than the paper size, or even than the number of prints in the final edition. For example, a postcard with two colors on the front and two colors on the back will be going through the press 4 times – while a large poster with only two colors is going to take half as much time on the press.
How does the printing of an edition proceed? For a two-color print, there will be two separate compositions created to use sequentially on the press. The first color of ink is put on the rollers with the corresponding portion of the design placed on the press bed, all of the sheets of paper for the whole edition are printed and put on the rack to dry. That first color of ink is then cleaned off the press. The compositional elements are rearranged on the press bed in anticipation of the next pass of ink which usually happens the following morning after the first pass of ink has dried. The prints are all cranked through the press again using the second color and put on the rack to dry again. On the third day, prints are stacked and given their final trim on the guillotine paper cutter.
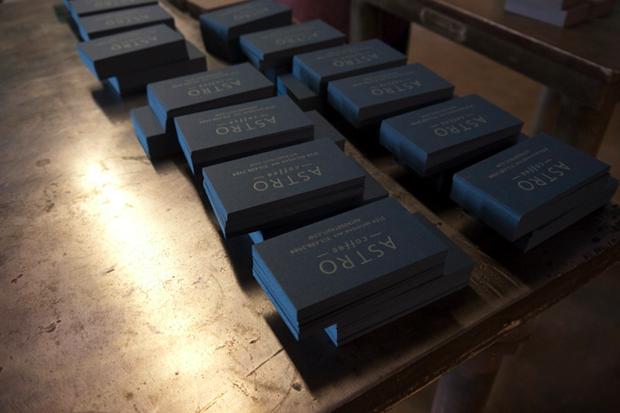
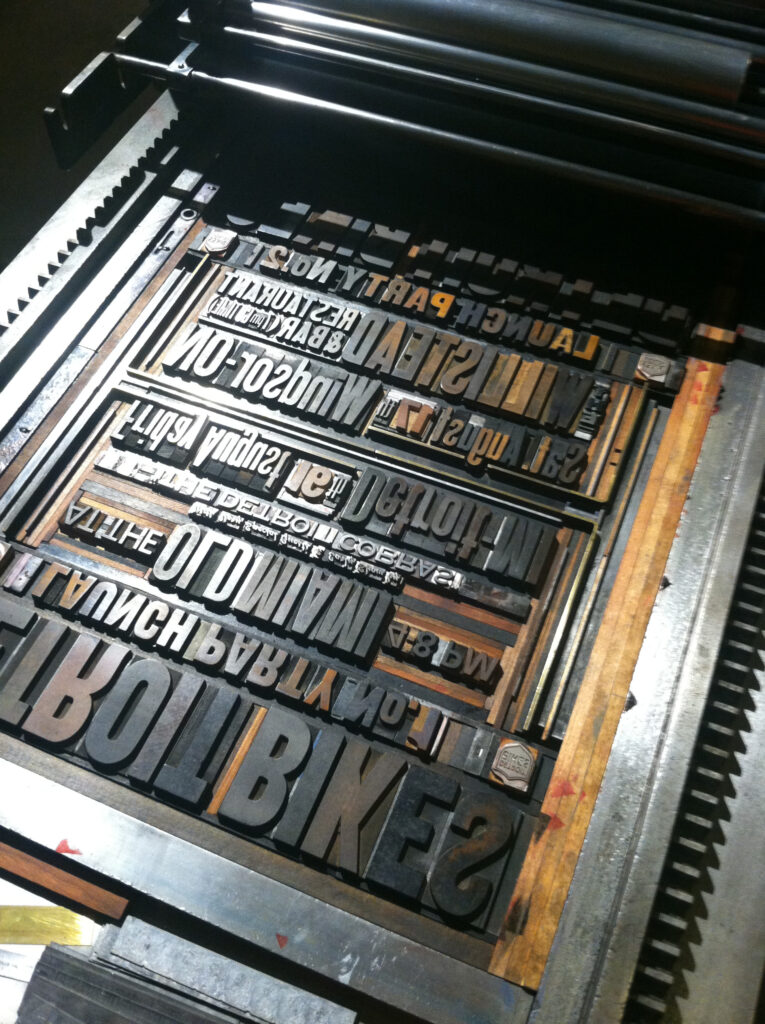